Cost optimization
The construction industry relies heavily on data for preconstruction planning, productivity enhancement, and risk assessment. Yet the industry's inherent complexities often lead to rework – the costly repetition of tasks due to design errors, poor workmanship, or inadequate planning.
The Misconception
Construction project management often focuses diligently on upfront planning and tangible metrics. But there's a dangerous blind spot: the ongoing, insidious costs of rework. Contractors meticulously track budgets and materials but are blindsided by rework's hidden effects. It's like fretting over a leaky faucet while the basement quietly floods – missed deadlines, damaged trust, and dwindling morale are the unseen water damage.
Rework Costs That Go "Unnoticed"
The direct costs of rework – wasted materials, additional labour, and equipment rentals – are painfully obvious. However, these are just the tip of the iceberg. Underneath lurk indirect costs that can eat away at profits and reputations:
Project Delays: Every rework cycle disrupts the flow, leading to costly delays. These may trigger penalties or even legal disputes with clients.
Damaged Client Trust: Nobody appreciates projects that run overtime and over budget. Repeated rework erodes trust and can damage future business opportunities.
Morale Drain: Reworking the same task demotivates workers, leading to frustration and reduced productivity. This affects overall workforce efficiency.
Increased Supervision: Rework necessitates tighter supervision to prevent repetition, increasing overhead costs.
Tarnished Reputation: Companies known for frequent rework struggle to attract top talent and win competitive bids.
These cascading consequences ultimately make the total cost of rework far greater than the sum of its visible parts.
The Tech Paradox
Despite advances in construction technology, why is rework cost management still an elusive goal? We deploy drones, robotics, and AI, yet grapple with the age-old monster of rework. The hidden costs slip through the cracks of our digital tools. Perhaps true innovation lies not only in new tech but in rethinking how we track and prevent these insidious losses.
Real-World Evidence and Statistics
The true impact of rework isn't theoretical; it's reflected in staggering numbers. Industry studies paint a troubling picture:
Communication Breakdown: Autodesk and FMI data reveal that in 2018 alone, poor project communication and data issues led to $31.3 billion in U.S. rework costs – a shocking testament to the need for transparency and collaboration.
Design Flaws: Up to 70% of rework stems from design errors and inconsistencies. This highlights the importance of meticulous upfront planning and clash detection to minimize expensive downstream fixes.
Total Cost Drain: Rework isn't just about replacing materials. When factoring in indirect costs, it can consume up to 9% of a project's entire budget, eroding profits significantly.
Why Rework Costs Stay Hidden?
Rework costs have a knack for slipping under the radar. This stems from several factors:
Inconsistent Tracking: Without standardised systems, rework events are often inconsistently documented or lumped in with general overhead, obscuring their true cost.
Data Format Barriers: Traditional spreadsheets and paper reports make it difficult to correlate rework across projects or identify recurring patterns.
Misplaced Focus: Project metrics often prioritize hard costs and schedule adherence, making rework data seem less relevant for decision-making.
Culture of Fear: Workers and supervisors may avoid flagging rework events due to fear of blame, perpetuating the illusion that rework is less frequent than it is.
This lack of visibility creates a blind spot. Without accurate rework data, management struggles to grasp the full magnitude of the problem and make informed decisions to address it.
Strategies for Reducing Rework and Managing its Costs
Tackling rework requires both technological advancement and cultural shifts within the industry. Here's a multifaceted approach:
Technology-Driven Prevention
VR/AR: Immersive technologies enable visualization of complex designs pre-construction, aiding in clash detection and reducing real-world surprises.
Drones: Site surveys and progress monitoring conducted using drones identify discrepancies early, preventing costly rebuilds later on.
AI and Computer Vision: These tools analyse vast image data for quality control, spotting errors or deviations before they become major rework issues.
Digital Collaboration: Centralised platforms keep everyone on the same page, version control limits confusion, and real-time communication quickly catches mistakes.
Process Optimisation
Lean Construction: Focusing on streamlining workflows and waste reduction translates directly to minimising the need for rework.
Enhanced Communication: Open communication channels across stakeholders encourage proactive problem-solving and pre-work planning.
Continuous Improvement Culture: Shifting away from blame and towards analyzing why rework happens fosters lasting solutions.
The Power of Data
Robust Project Data: Developing consistent rework tracking systems provides the foundation for better cost analysis and targeted improvement strategies.
AI and Machine Learning: Predictive analytics can identify patterns and highlight high-risk areas for rework, allowing for preemptive mitigation.
Important Note: Technology isn't a magic bullet. Effective implementation alongside a culture shift promoting quality and transparency is key to lasting success.
Reducing construction rework is an ongoing process that requires early action and understanding. Recognising common causes and swiftly addressing them can prevent costly overruns, missed deadlines, and dissatisfied stakeholders. By leveraging technology and digital tools, and adopting a tech-driven workflow and data-centric approach, you can proactively reduce rework and minimise its impact on your projects.
The goal is to avoid hearing "We must do it again!" by taking steps to ensure issues are spotted before they can happen.
Recent Post

Case Study
How a Leading Saudi Development Entity Reduced Evaluation Time by 85% with TruBuild

Announcement
TruBuild Raises $1 Million Seed Round to De-Risk Construction Projects and Prevent Cost Overruns
Apr 13, 2025
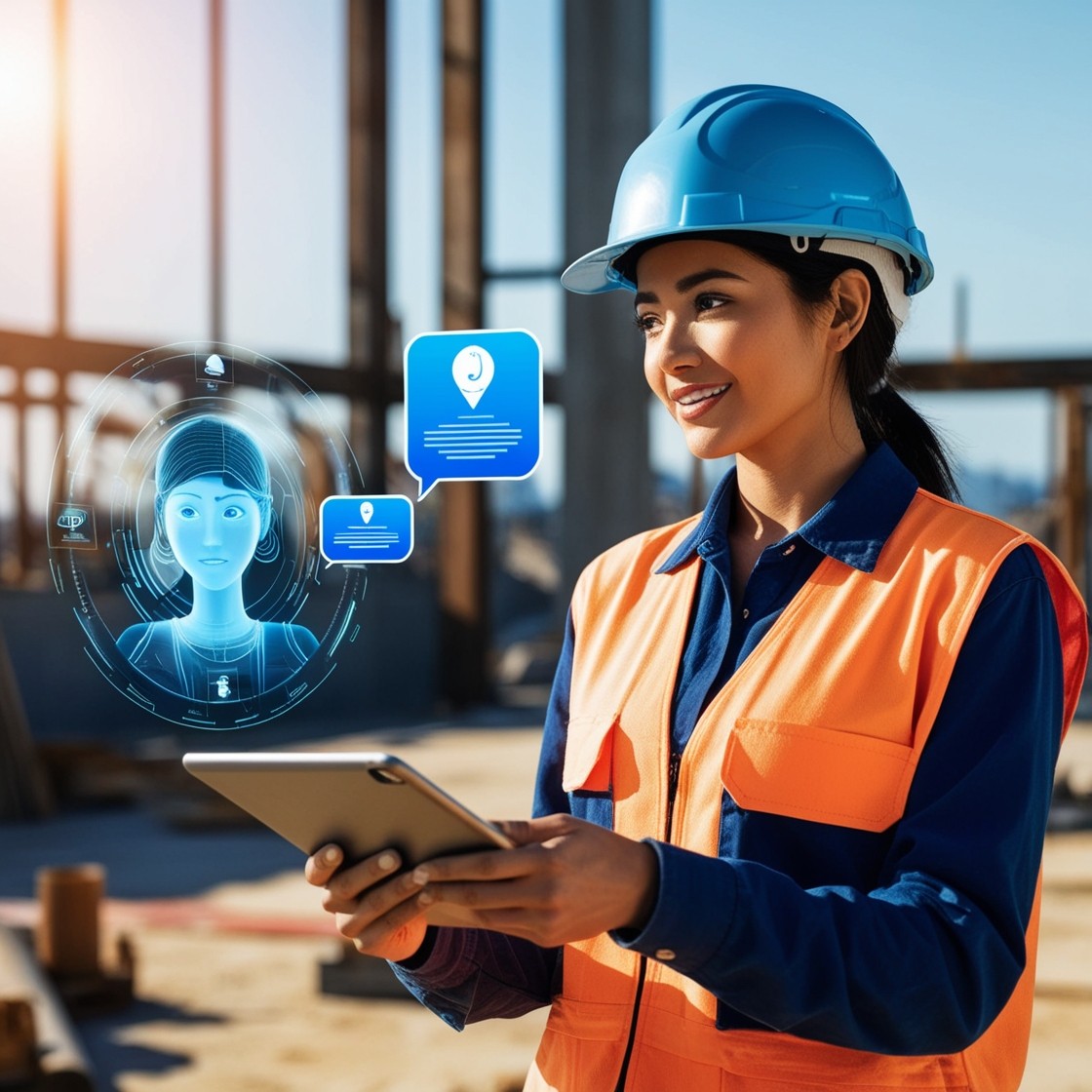
AI Assistant
The AI Assistant Your Construction Project Deserves
Aug 12, 2024
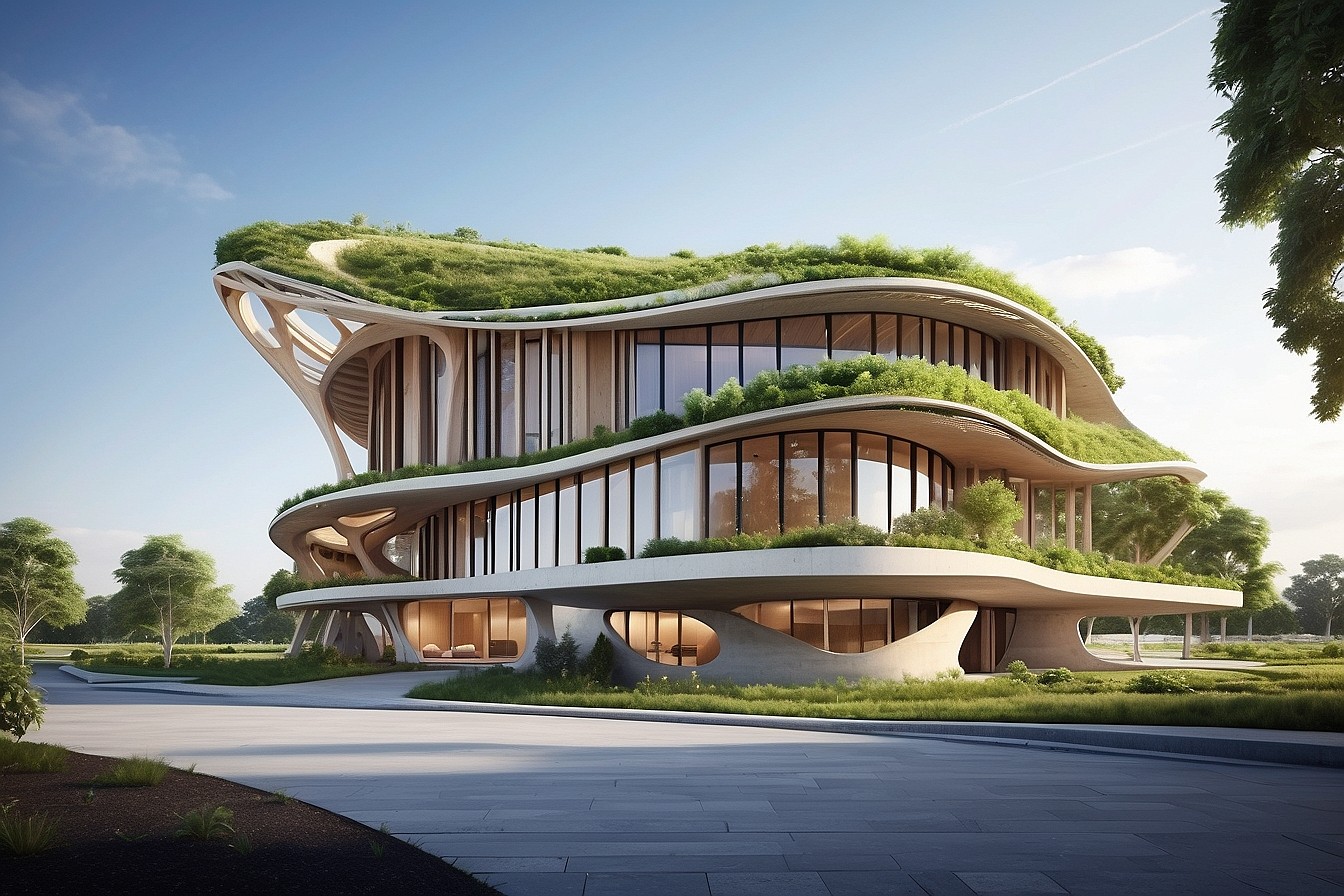
Sustainability
The Urgent Need for Sustainable Construction: Why It's Not Optional
May 25, 2024
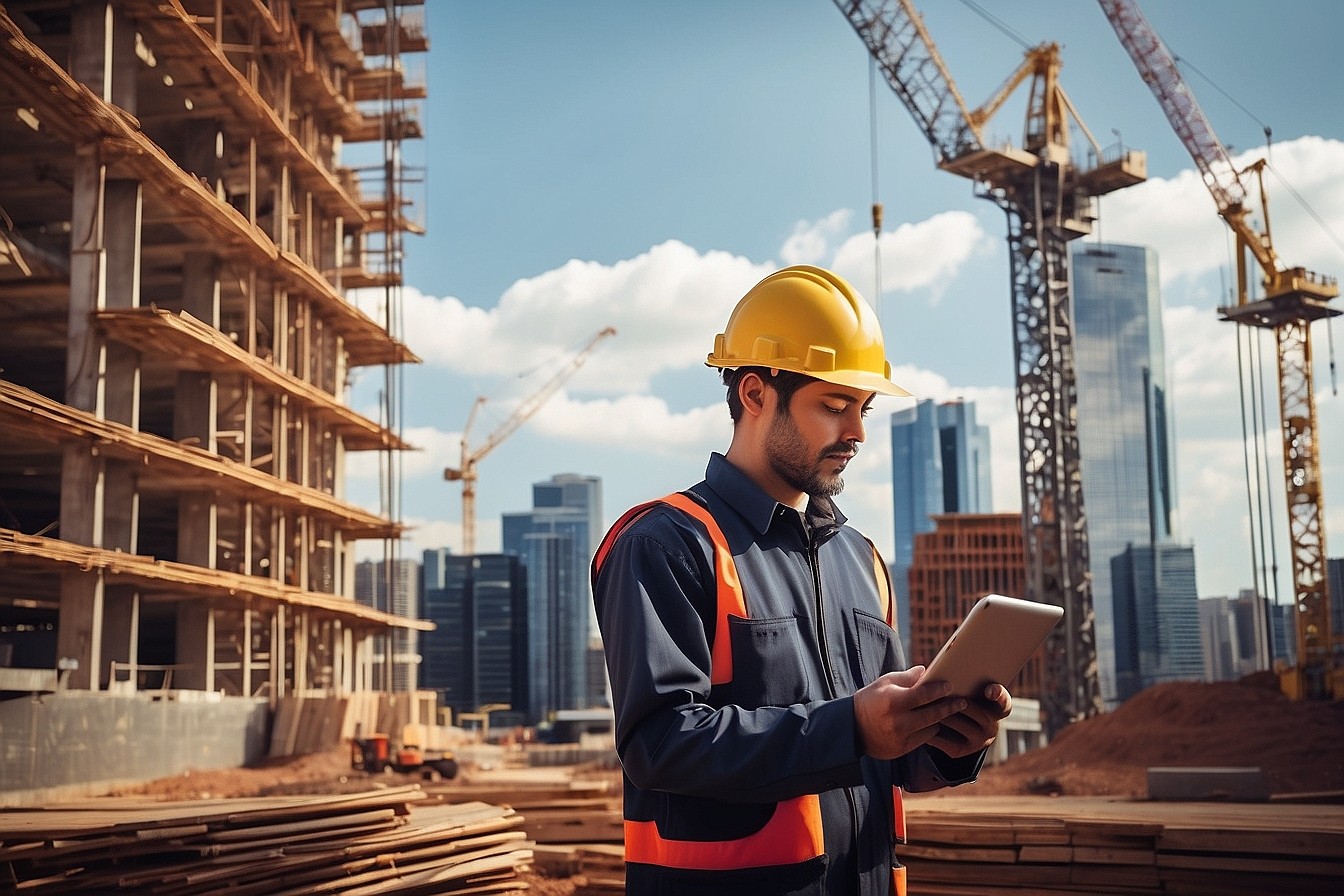
Cost optimization
The Hidden Costs of Construction Reworks: What You Need to Know Before It’s Too Late!
May 25, 2024
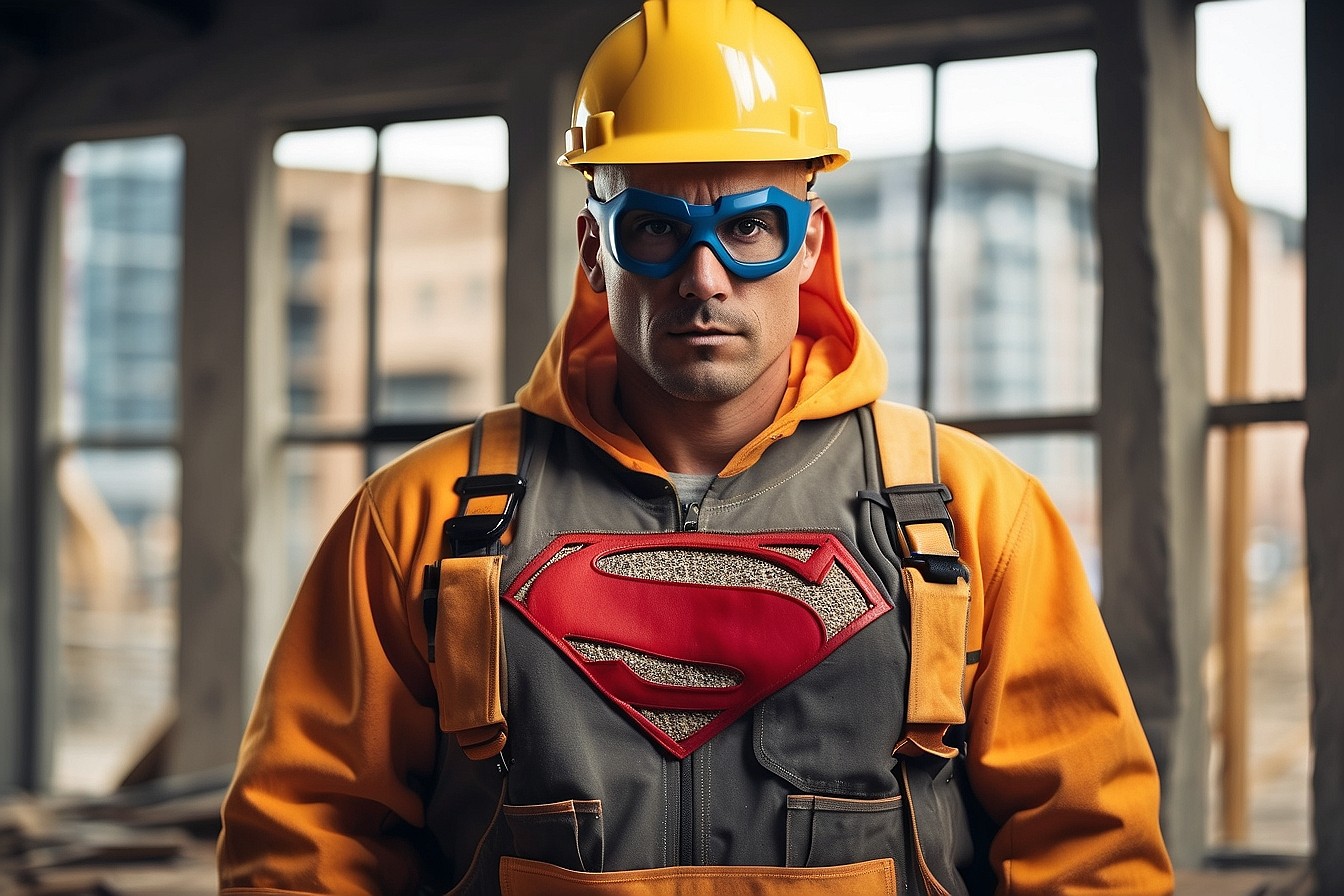
AI
Boost Your Construction Site’s Efficiency With These Genius Productivity Hacks!
May 25, 2024
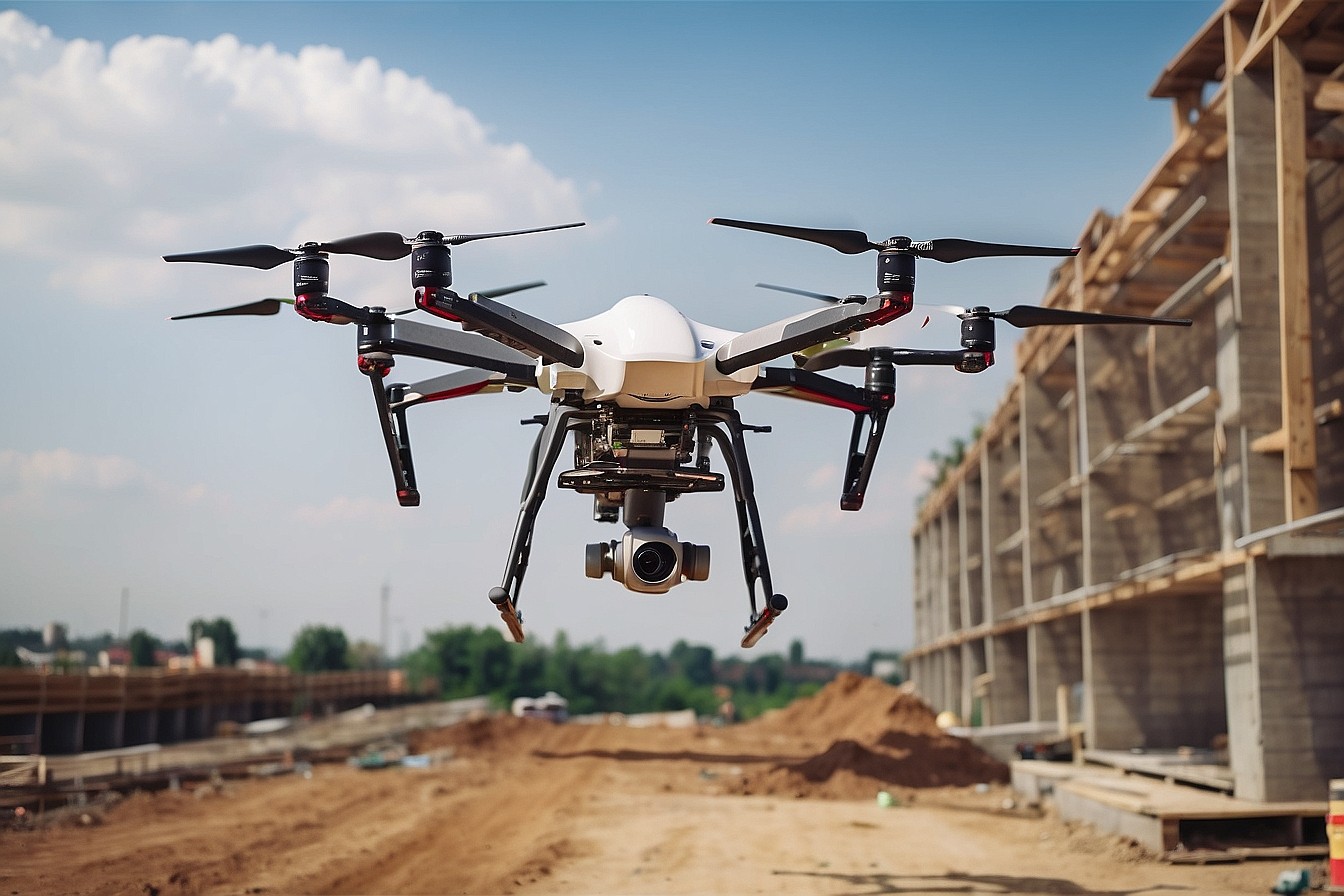
Augmented Reality
Technologies that are changing the construction industry
May 25, 2024